Just think about load paths mate.
On a cage like yours no tubes should be joining another mid run unless there's a corresponding tube to transfer the load path. The exception to this is in the corners, where it's transfered down the 2 adjacent legs.
If you have front turret supports to go forward from the front legs, I'd suggest they need to be inline with the upper and lower parts of the door bars so the loads are transfered through the whole cage.
One thing to be VERY careful of is elbow clearance too. If you sit very low you may well find it's tight on elbow room. I'd yeah fit a seat and check that before welding anything up.
Done a bit more digging with they're photos they've supplied and although the CAD drawing they supplied shows them meeting at the same point on the A pillar upright the pics of one installed suggests differently which is strange??
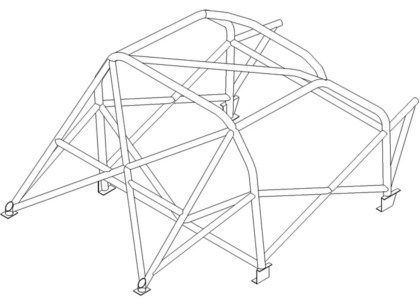

Excuse the poor quality of some as when I opened the cd with the pics on the computer I just took a load of photos on the phone of the screen for reference

Also either I or they have made a monumental **** up and got the pass side door diagonals the wrong way round as the drivers side suggests the longer bar is at the bottom lol


I have tried to work out the rough seating positions but found it quite hard without some kind of subframe and steering wheel etc to gauge from
At the moment I think I'll probably trim the bottom tube and fit something like this

As you say if the top front turret support is as near to the bend as possible then should spread the load a bit more evenly along both directions, although due to the lower support would expect it to be directed a bit more up the top section?